WATER PRODUCTION IN THE MATURE FIELDS OF THE NORTH SEA CAN BE 90-95% OF TOTAL FLUIDS PRODUCTION
In 2018, water production accounts for 90-95% of total fluids production in mature fields of the North Sea. It is not uncommon for fields producing 10-15,000 barrels of oil a day to produce over 300,000 barrels of water. Reducing water production would go a long way to improving field economics:
Reducing the water cut in a well reduces the density of the column of flowing fluid, increasing the draw down and improving the flow rate.
Many topside facilities are constrained by water production - the facilities can’t take anymore fluids so wells that could produce some oil are cut back or shut in.
In heavy oil reservoirs the viscosity of the crude oil can be significantly greater than water, so water breakthrough will rapidly result in water coning and a rapid drop off in production rates almost as if someone turned the oil off.
It costs money to inject seawater, but in many fields injected water merely goes through the reservoir coming out at the production well without having displaced any oil.
Various scenarios that reduce the economic recovery of a well can be explained:
Wells are drilled horizontally to improve production rates, when water breaks through particularly in the “heel”, zonal isolation proves challenging
Many wells produce from separate and discrete zones or intervals and often it is the high permeability zones that suffer water break through first – “drowning out” oil production from less permeable or lower pressure zones.
The Oil & Gas Technology Centre (OGTC) estimates that in the UKCS excess water cut or liquid loading is the third largest cause of well shut-in and production loss. Reducing or shutting off water production in wells improves production, reduces operating costs and increases recovery rates by extending life of field.
Mechanical techniques such as bridge plugs or straddle packers are an accepted proven technology for water shut off and put simply result in a “patch” over part of the perforated interval, sealing off the water producing zone. Such an approach requires a workover or the deployment of a work string. Based on operator feedback, existing technologies can have potential drawbacks;
The bridge plug or straddle seal can fail
A micro annulus can be created in the annular cement resulting in water bypass
In many old wells, the casing string has been damaged resulting in water bypass
At best, mechanical water shut off is a temporary solution – the water comes back and it can make things worse by near well bore water coning into previously dry zones, resulting in reduced recovery rates.
Mechanical water shut off treatments on old wells are difficult, technically challenging and expensive, making it difficult to make an economic case for them in late-life field developments . An approach that deals with water bypass issues more reliably, easily and is simple to apply, is required.
Chemical water shut off application generally involves mixing a fluid at the surface and then pumping it into the well where a reaction takes place and a gel or a deposit is created which forms a barrier preventing water inflow.
A successful chemical water shut off system should have the following characteristics:
The chemistry of water shut off is clearly understood and can be applied simply in the field.
There needs to be a way of stopping the water shut off chemical from entering oil producing zones.
The water shut off barrier should not be a patch creating the risk of coning but should rather create a barrier within the reservoir.
Chemicals used should be safe to use and environmentally acceptable.
Aubin’s XMAX technology is a new approach to water shut off which combines fluids to form an insoluble inorganic scale within reservoir pore throats, stopping water from entering the well. It has been described as “doing a scale squeeze backwards” instead of preventing scale we are making scale in the reservoir in a controlled and targeted manner.
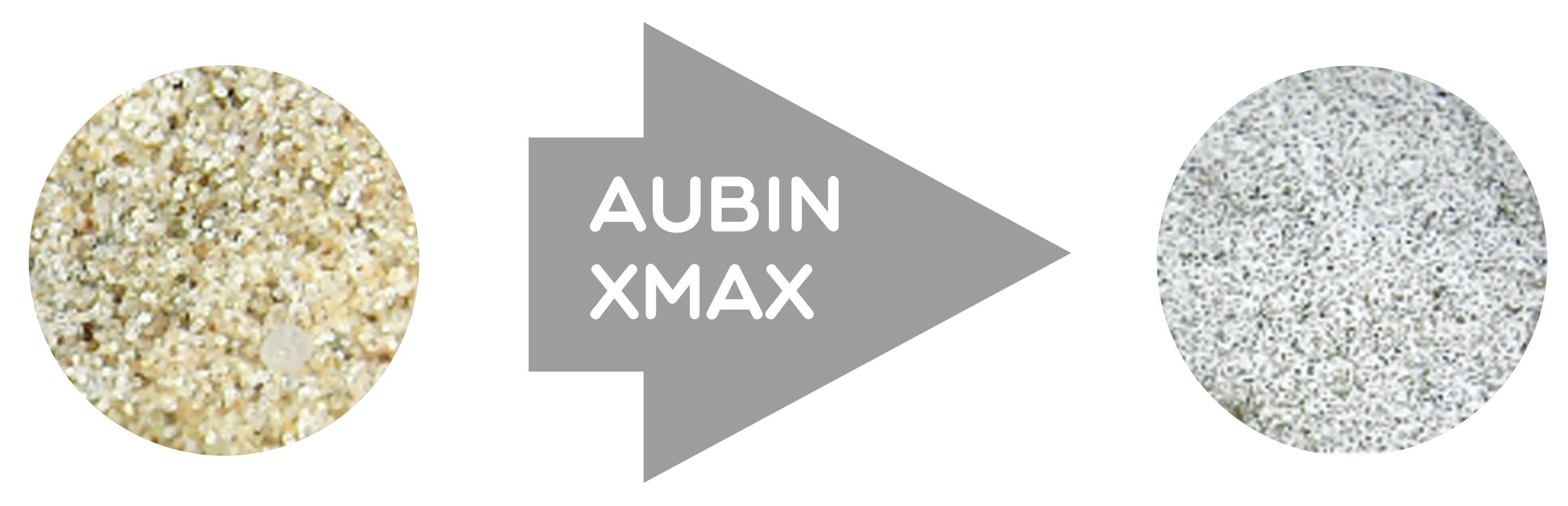
Put simply, two fluids are mixed offshore and pumped into the well where they are delivered to the water producing zone either by existing straddle packer technology or by chemical isolation techniques. One fluid is a source of Calcium ions, the other a source of Sulphate ions. When mixed together these fluids react to form insoluble Calcium Sulphate scale. This reaction is controlled by an inhibitor which stops the fluid scaling when pumped down the well. Once the fluid gets into the formation it gets hot and the scale reaction occurs depositing insoluble scale in the reservoir. Tests by scientists at Heriot Watt University show permeability reductions of over 90%.
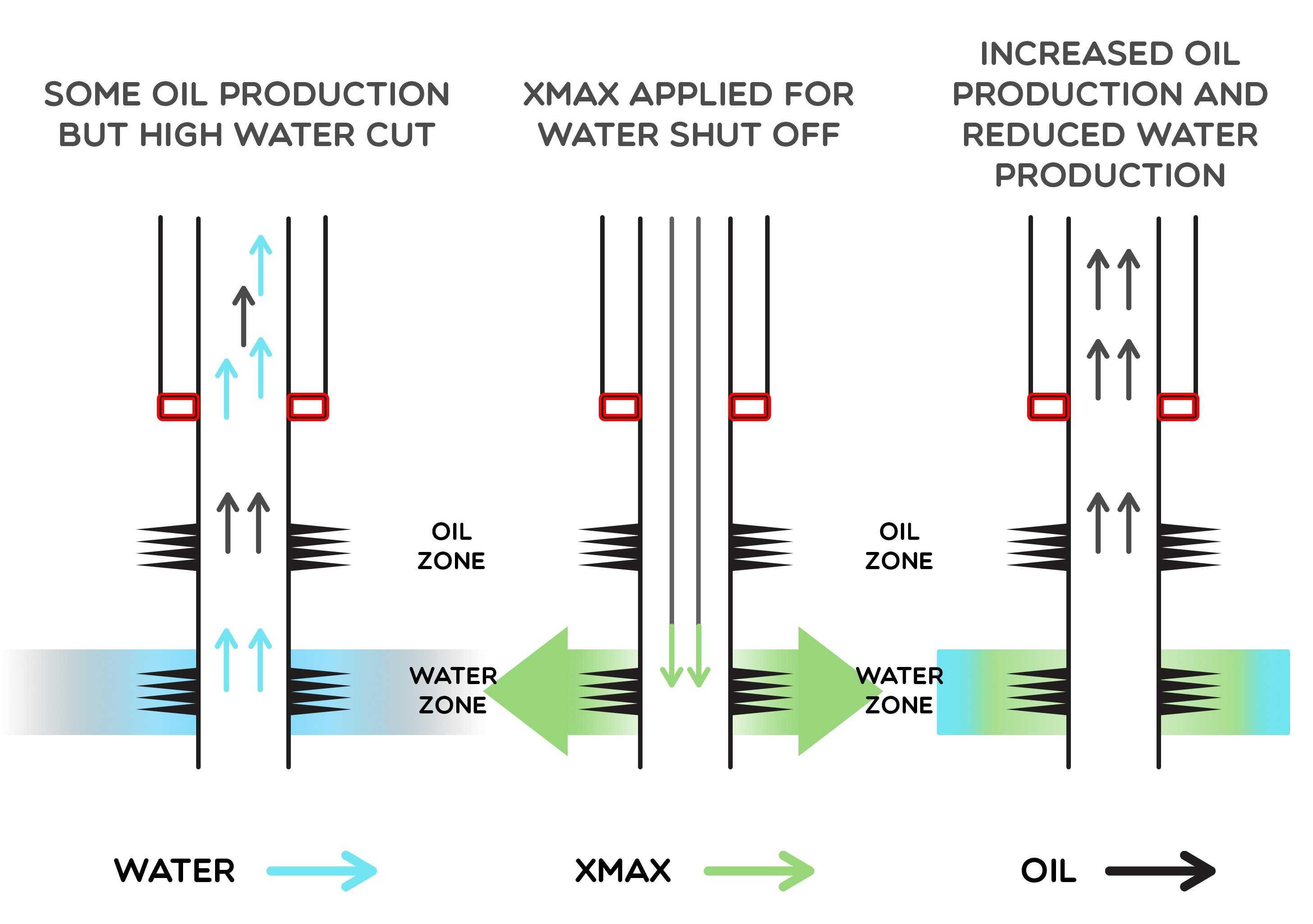
There are some wells where mechanical water shut off techniques can’t be used. One such example is horizontal wells with water ingress at the heel. Treatment with XMAX simply requires installing a retrievable plug to protect production from the toe and then pumping XMAX into the heel section shutting off water production and finally retrieving the plug. Alternatively, XMAX could be used prior to or instead of refraccing unconventional wells.
XMAX offers a precise, risk-free means of isolating water production by creating a barrier in the reservoir. Deployment is simple and requires no additional equipment by utilizing similar practices to common acid stimulations or chemical treatments.
XMAX can unlock increased hydrocarbon production in your well by targeting zones and progressively managing water production over the life of a field, resulting in improved economics and enhanced levels of recovery.
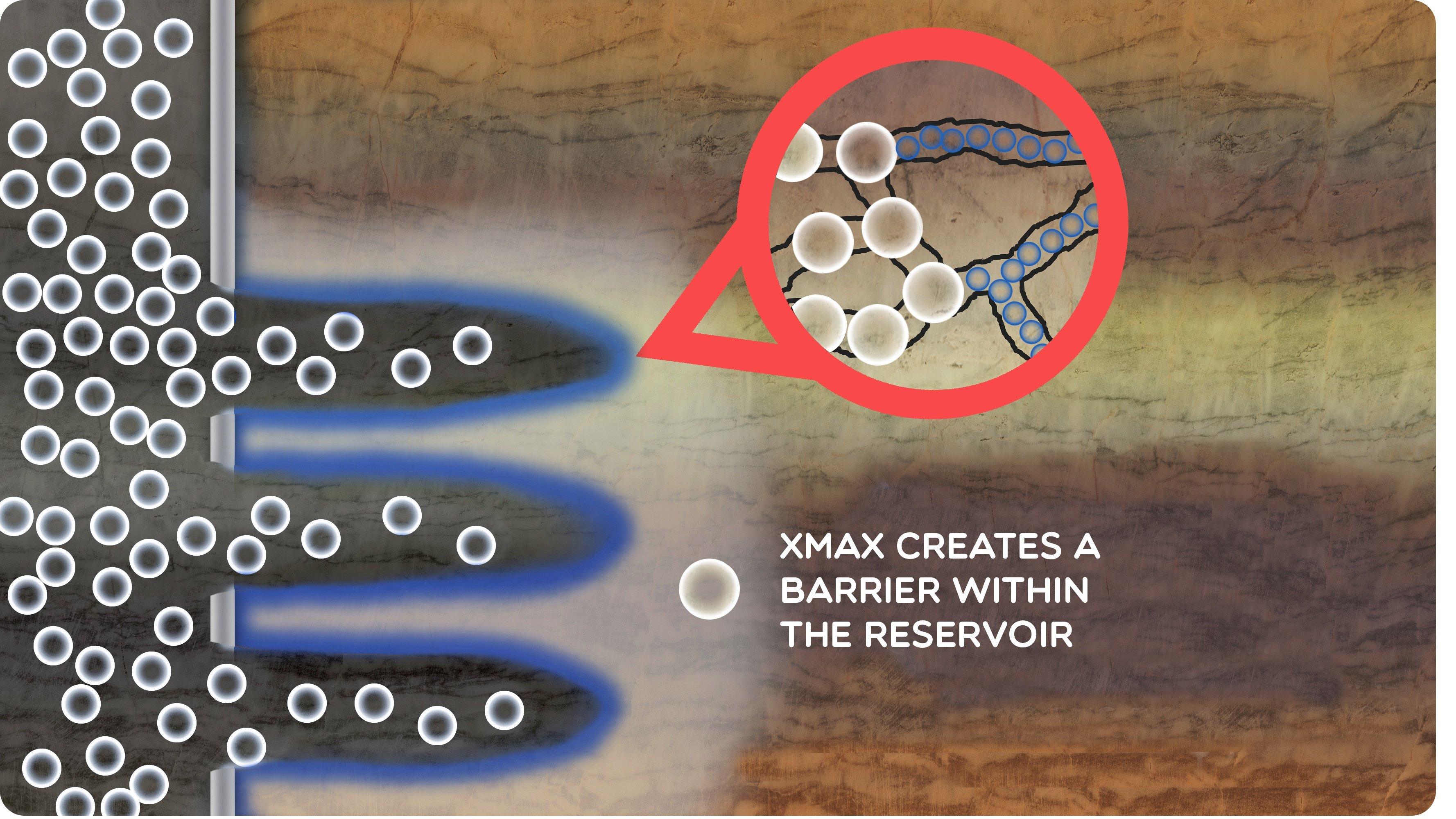