1. When was the core range of foamers created?
“The initial seed was planted following a gas well deliquification conference that the team attended in 2013. Building on the knowledge we already had and taking the new learnings on board, we recognised we had the technology to create a product that would solve a problem many companies within the industry faced.
“Decreases in pressure and the reduction in gas velocity can lead to liquid loading within the well; resulting in reduced production and eventually end of life for the well. The chemical foaming agents all help to reduce the liquid and maximise production as a result, while minimising the need for mechanical lift.
“Within 12 months we had developed a few products which formed our core range of foamers. We did have some foaming technology prior to 2013 that was centred around stimulation, which we have improved in recent years, however, our range of foamers are more tailored to production enhancement now.”
“Within the Aubin® range, there are 6 core chemical foamers, however, each one can be tweaked and adjusted to meet the needs of our clients and the conditions they’re operating in.
“For instance, Aubin® SFA-03, Aubin® SPA-04, Aubin®SPA-05 and Aubin® SPA-06 are very similar in that they are suitable for water depleted gas wells for temperatures of up to 100°C, low or high salinity levels and can be applied either in batches or continuously. However, their dosage requirements are different - Aubin® SPA-03 can vary from 3,000 to 20,000ppm, whereas Aubin® SPA-04 is from 1,000 - 20,000ppm. Aubin® SPA-05 and Aubin® SPA-06 can also be used to unload water and condensate with a dosage from 3,000 - 80,000ppm.
“Our higher performance foaming agent is Aubin® SPA-07, which can be used in similar settings to the rest but can be applied in temperatures of up to 170°C, and is more effective in a higher condensate cut than Aubin® SFA-03 to 06. Finally, Aubin® SFA-10 is our newest foaming agent which launched in 2020/1, it can achieve high foam quality and stability and has had a number of applications in mainland Europe.”
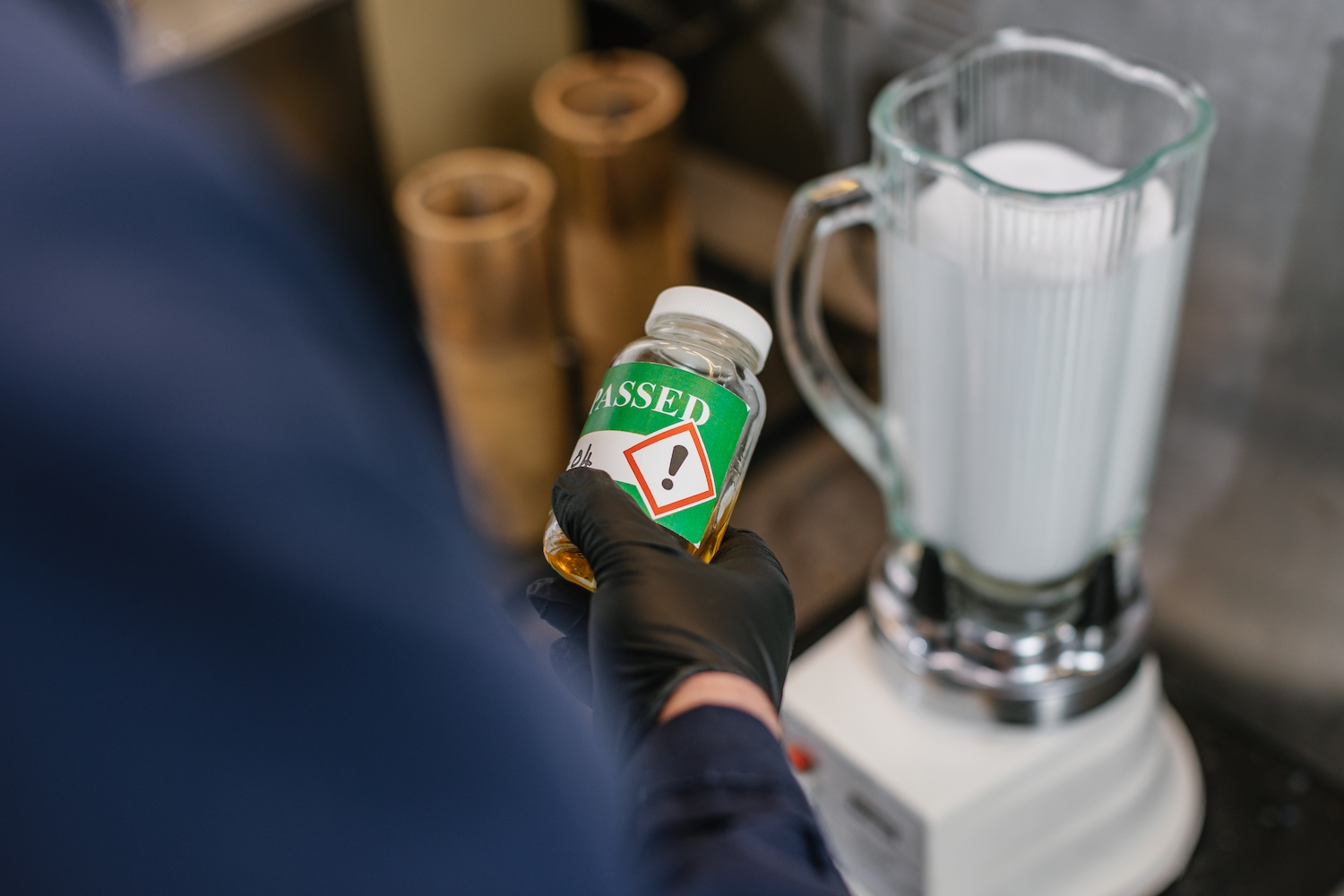
3. Why are there different types of foamers and under what conditions do they need to be applied?
"There are a few conditions to consider and choosing the right foamer is not always an easy process, so we can carry out foamer testing if our client can get representative samples for us to analyse - this is something that we’re doing at the moment for some of our customers to help them choose the right one for their well’s conditions.
“The main factor to consider is the varying temperatures of gas wells, which is why we’ve developed a range of foamers to be applied depending on the temperature they’re required to withstand.
“Foamers might be used in a system where people are worried about discharge of water later if they’ve got a separation system. Most foamers are surfactants so there’s a high chance that they’ll go into the water phase, you probably want to avoid using them in a system where someone is likely to discharge the water afterwards for environmental reasons.
“The ratio of hydrocarbon to water can be another factor when deciding which foamer to use, as well as the ratio of any other additives used to treat gas wells. If someone is adding methanol into their well, for example, that might impact foamer performance.”
4. Why are chemical foamers better than alternative methods?
"The most significant benefits of our chemical foamers is that they are cost-effective and safe to use - which are arguably two of the most important considerations when it comes to any operation.
“By applying a foamer, you’re not introducing any integrity risk in the same way you would using mechanical lift. Depending on the type of well, you might need to assess the impact on well formation and identify whether or not the well has the infrastructure to inject a foamer, but to date when used and tested, Aubin products have demonstrated no formation damage and have a relatively low environmental impact, as they use biodegradable and/or low ecotox and/or PLONOR raw materials.
“Chemical foamers also provide significant cost savings for clients too. They’re a far more cost-effective solution than mechanical lifts, and maximise the operational lifespan of a well by removing liquid build-up which prolongs the need to spend money on plugging and abandonment.”
5. What is an important consideration when it comes to applying a chemical foamer?
"For a longer term solution, it is key to understand that when you’re looking for a solution to deliquify a well it is always best to understand why you have liquid loading in your well in the first place. For example, it might be that you need to clean up perforations due deposits of scale which result in a lower pressure in the well; that could be a cause of liquid loading and may make all deliquification efforts relatively pointless unless you treat and prevent the cause (e.g. chemical clean-up and appropriate scale inhibitors design). It may be that the fluids are coming from an integrity issue in casing - perhaps they are made up of completion fluids and not from the formation! Where you have little to no information in the origins of the liquid loading, or where you have detailed information on the fluids and on the cause of the problem, chemical foamers can often be a quick and low cost solution to increase production.”
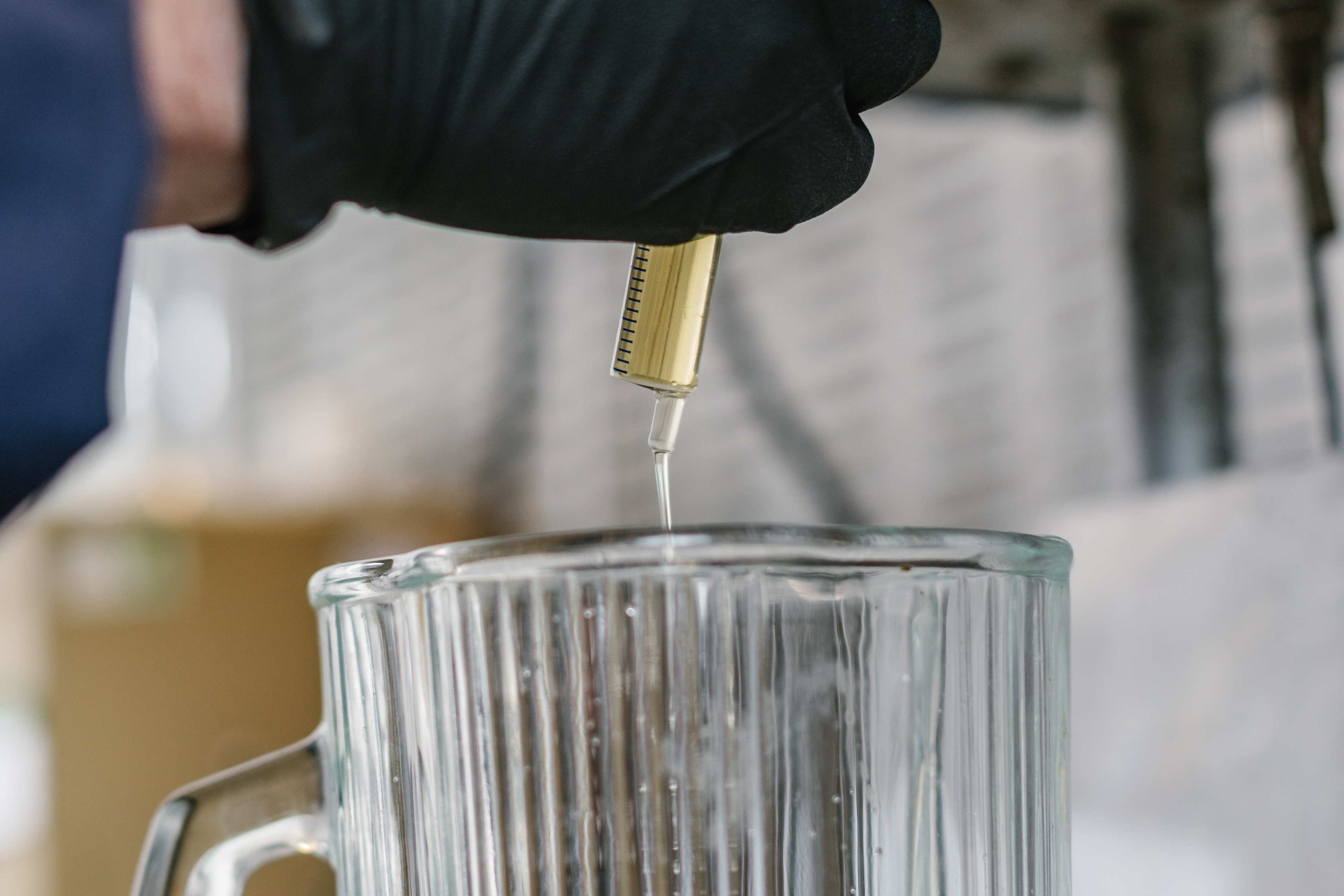
6. Are there any key success stories you can share around Aubin®’s chemical foamers?
“We completed a project in South Africa using an Aubin® foamer. The company had no usable infrastructure in place on their subsea well and the pressure of the well was completely depleted, so they had to spend approximately $1m to install tubulars and nitrogen after the foamer was applied to provide additional gas to lift liquid (which is more expensive than our normal foaming treatment requirements). However, they achieved over $15M dollars of recovered hydrocarbon from a previously dead well, so the return on investment was huge. Additionally, we supported the pre-qualification of our system, including tests that demonstrated impact on formation through supplying our chemical for third party core flood experiments.
“We have had a lot of success in the North Sea with our range of chemical foamers, and are now starting to see them be used in Norway as well which is great. We have an ongoing project that has included technical support from our Aberdeenshire lab using Aubin® SFA-04 to simulate deployment scenarios for an offshore gas storage facility.”
7. In your opinion, what is the future of Aubin® foamers?
“Our research and development for chemical foamers has focused a lot on the environmental side of things. Aubin® SFA-07 is a high performance foaming agent but it hasn’t yet been benchmarked in its eco qualities, so we’re starting to evaluate this and intend to make improvements (if required) following our assessment.
“As our newest chemical foamer, Aubin® SFA-10 is receiving steadily growing interest in mainland Europe, as it addresses temperature application concerns for our client in this region, so we’re hoping to see this growth continue.
“We’ve always been interested in using chemical foamers for stimulation - it's where our foamer expertise lay before 2013, when we started to focus on production enhancement. I think, in the future, we might look to develop more foaming agents that promote stimulation and develop that side of the products further.
“Since being acquired by ItalMatch, we now have huge manufacturing capabilities and access to more global operations. I’m looking to introduce the Aubin® product range with colleagues in North and South America, which will allow us to bring our chemical foamers to more projects with a wider regional scope.”
To learn more about the Aubin® range of chemical foamers, please visit our Foamers web page by clicking here.