Unwanted water production is one of the biggest challenges when looking to optimise hydrocarbon production from a well, and for many years our team has been researching, investigating and testing potential solutions.
In this blog post, Lindsay Wylie, Project Manager for Well Technology, shares insights and data around this major problem our industry faces, and discusses a solution that we have developed to enable water shut off downhole, and in turn improve field economics and create value for operators.
THE PROBLEM: OVERPRODUCTION OF WATER
“The oil industry is producing increasingly staggering amounts of water, to the point where it is becoming known as a water industry. Across the world, the daily production of water is 5 bbls for every 1 bbl of oil, which has huge implications for companies.
“As the volumes of produced water increases, the cost of handling it also increases through processes such as separation, filtering, pumping and reinjection. Eventually, the cost exceeds the value of the associated oil, which can lead to premature well abandonment.
“In a recent Oil and Gas Authority (OGA) study, it was identified that 20% of wells shut-in in the UKCS had water production issues, the second biggest issue after well integrity. The study also found that based on current methods, the estimated water shut-off cost is only £3.40 per bbl of oil.
“The issues that arise from water production have proven to be incredibly costly for companies operating in the oil industry, and demands that an alternative, more cost-effective and more effective solution be identified for water shut off.”
A SOLUTION: CREATING A BARRIER IN THE RESERVOIR
“To overcome the problem of unwanted water production, we have developed an innovative product that simplifies the solution by using a well understood reaction, a straightforward treatment programme, and established deployment methods.
“Xmax enables water shut-off by reducing the permeability in the near wellbore formation, thus preventing the inflow of water. The solution is pumped into the reservoir, where it forms a stable mineral precipitate which blocks the pore throats of the formation rock.
“The chemical reaction is controlled to ensure the mineral does not form until it enters the reservoir, rather than in the well.
“By tackling the problem in the reservoir rather than in the wellbore, issues caused by the formation of micro-annuli and water bypassing is reduced.
“Xmax was independently tested by Heriot Watt University and supported by OGIC, with coreflood testing. The results from coreflood testing demonstrated a permeability reduction greater than 85% within 5 pore volumes.”
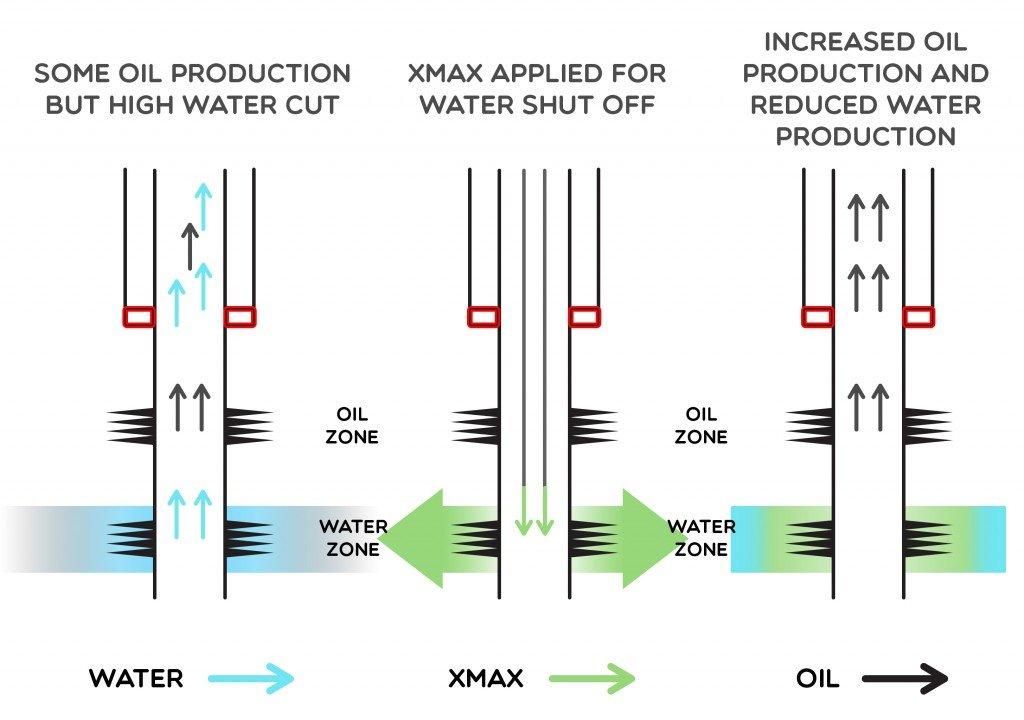
THE BENEFITS OF XMAX
“The credibility of Xmax is further supported by its numerous benefits and simple application to enabling water shut-off successfully, while keeping costs lower than traditional water shut-off technology. The key benefits of Xmax are as follows:
Uses non-hazardous chemicals to form a stable mineral in the pore throats of the formation.
Reduces permeability deep within the reservoir, avoiding water bypass issues common to wellbore methods.
Full wellbore diameter is maintained following treatment.
Deployed using standard well intervention technologies, making it a widely applicable and straightforward product to deploy."
Register your interest in Xmax, our innovative chemical water shut-off treatment, by completing the form below.